Destilliergeräte zur Destillation brennbarer Lösemittel dürfen, wenn sie nicht im Freien aufgestellt werden, ausschließlich in Räumen oder Bereichen • die den Anforderungen an explosionsgefährdete Bereiche der Zone 1 entsprechen • und innerhalb derer eine in Bodennähe wirksame Lüftung die Bildung einer gefährlichen explosiven Atmosphäre verhindert (= primärer Explosionsschutz) betrieben werden. Die Anforderungen zum Schutz gegen Explosionen gelten als erfüllt, sobald die elektrischen Betriebsmittel den Erfordernissen der Zone 1 (C1) entsprechen (= sekundärer Explosionsschutz). Zone 1 ist ein Bereich, in dem damit zu rechnen ist, dass explosionsfähige Atmosphäre als Mischung brennbarer Stoffe in Form von Gas, Dampf oder Nebel mit Luft bei Normalbetrieb gelegentlich auftreten kann. Der Gefahrenbereich, innerhalb dessen alle notwendigen Vorkehrungen gegen Explosionen getroffen sein müssen, dehnt sich wie folgt aus:
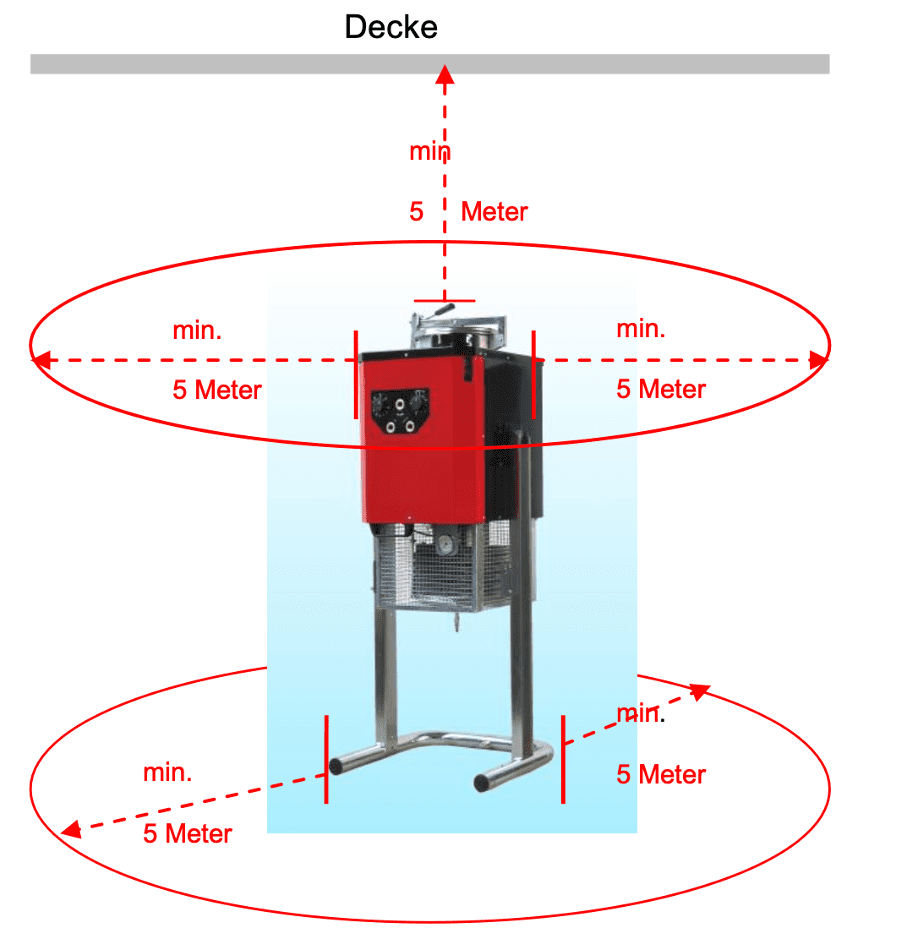