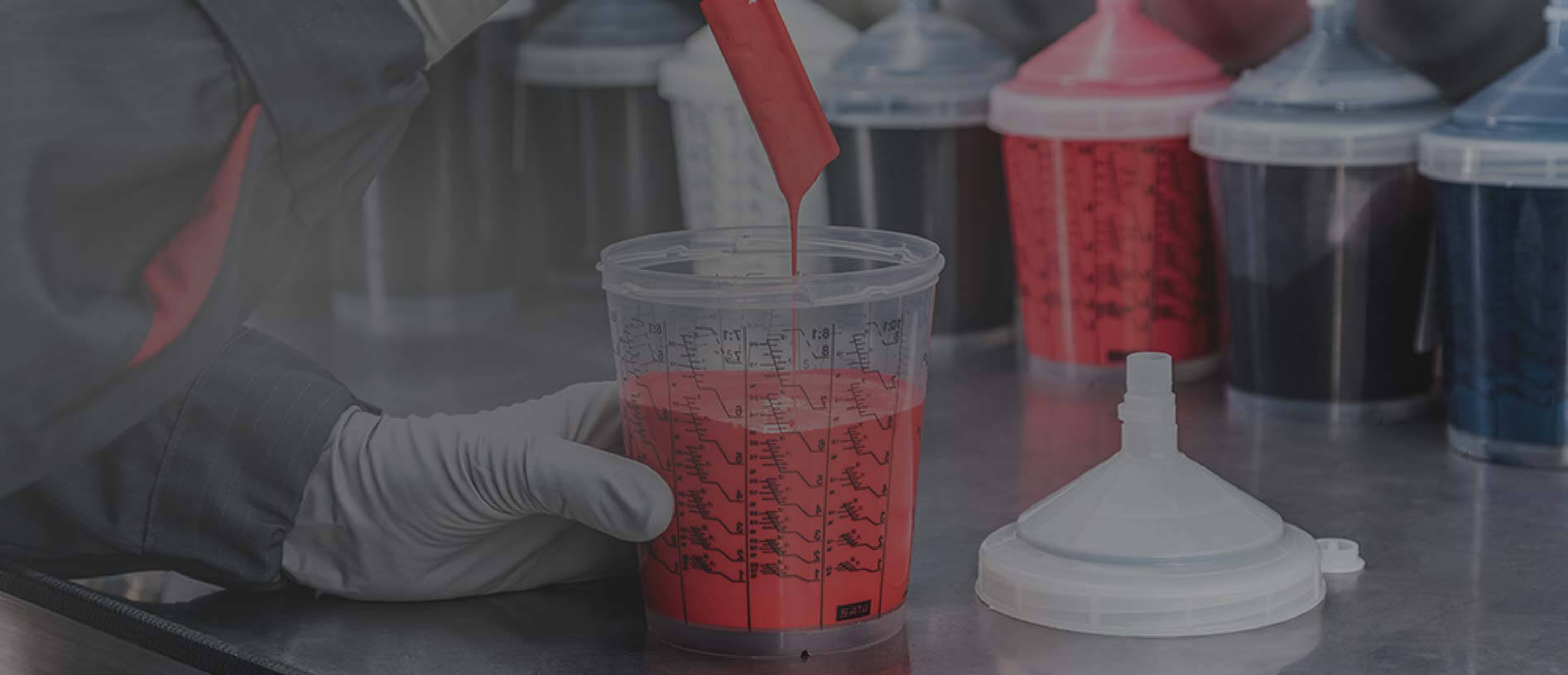
Distillation plants
We offer you excellent distillation equipment and distillation units for solvent recovery.
Distillation plants
We offer you excellent distillation equipment and distillation units for solvent recovery.
Filter products
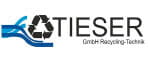
Price excl. VAT
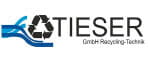
Price excl. VAT
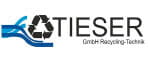
Price excl. VAT
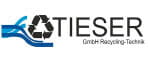
Price excl. VAT
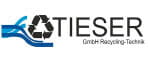
Price excl. VAT
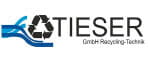
Price excl. VAT
Distillation apparatus, Tieser solvents
We offer you excellent stills and distillation units for solvent recovery.
With more than 7,000 solvent recovery systems delivered, Tieser has become the market leader in the field of solvent recovery systems.
Description of distillation unit
The distillation units for solvent cleaning are designed according to international safety standards that apply to a distillation apparatus.
Every single still, distillation apparatus and distillation unit is certified by authorised testing centres. The outstanding quality standard of the distillation units for solvent cleaning is significant.
As a customer, you can be sure that each solvent recycling unit has been individually tested. Every solvent distillation unit comes with an instruction manual for easy operation. In addition to the many different types of distillation units for distilling any solvent, we also offer you a custom distillation unit for cleaning solvents.
How does a distillation unit work?
- The Tieser distillation unit from the Dlstatic series is used to recover contaminated solvents. This distillation unit separates contaminants such as resins, oils, varnishes, etc. from the original solvent.
- The vapours produced during solvent cleaning in such a distillation unit pass into a condenser, and the condensed solvent is collected in a container for reuse.
- A film bag collects solid impurities. This film bag is heat-resistant and also solvent-resistant, making it ideal for our distillation systems.
- We also supply every distillation unit as a vacuum distillation unit, according to customer requirements.
- Every single recycling unit for solvents from this distillation device series is available as a 12, 25 or 60 to 180 litre distillation unit.
Distillation units with stirrer
The solvent distillation units in the Dynamic series are another series of distillation apparatus. This recycling unit for solvents is used to process various solvents with boiling points between 50 and 240 degrees. In this distillation apparatus, the solvent is cleaned by an optimised agitator. The operating cycle of this distillation unit for solvent cleaning is fully automatic, so that an employee is only required occasionally at this solvent distillation unit.
The distillation units for solvent cleaning for industrial use have an internal scraper/agitator to prevent adhesion to the boiler in the distillation apparatus. Each boiler of the distillation apparatus is made of stainless steel, which guarantees a long service life. Due to the optimised ratio of boiler depth to boiler diameter, this distillation unit for solvent cleaning guarantees perfect distillation. Another advantage of this solvent distillation unit is the easy emptying of each distillation apparatus due to the integrated tilting option.
With every distillation unit, the solvent properties are not changed to the disadvantage by the solvent cleaning. Therefore, the process of solvent distillation can be carried out as often as desired in a solvent distillation apparatus. For this reason, all solvent distillation units are made of the highest quality materials, which means that the solvent distillation apparatus has a long service life. In addition to distillation equipment and industrial distillation plants, we offer our customers further products (such as evaporators) for processing. All products meet the same standards as every solvent distillation unit and every solvent distillation system.
Operating overview
Properties
TIESER distillation units enable the recovery and reuse of solvents used for cleaning and degreasing in a wide range of applications. By exploiting the simple principle of distillation, the impurities (resins, pigments, paints, ink, oils, solids, etc.) are separated from the solvent, which is collected in a container for subsequent reuse.
The contaminants settle on the bottom of the kettle and are then simply emptied over the previously inserted plastic bag.
The solvent properties are not changed by the distillation, so the distillation process can be repeated as often as you like.
Operating principle
The boiling of the contaminated solvent takes place in a vessel made of stainless steel AISI 304. The uniform heating is achieved by a heating jacket made of heat transfer oil, which is heated by one or more heating rods.
The solvent vapours produced are conducted into an air-cooled condenser, which is available in copper or stainless steel.
The condensed solvent is then collected in a container.
All devices are tested for leaks. This ensures that no oil or solvent vapours escape during operation.
Operation
The distillation cycle runs automatically. The presence of an operator is only required for filling, setting the temperature and the distillation time and for emptying the solid and liquid residues.
Cleaning
Emptying the residue and then cleaning the device is completely hassle-free:
Simply tilt the device to empty liquid residues.
For solid contaminants (varnishes, resins, polymers, pigments, etc.), use the plastic bag.
The end product is a residue that can be disposed of easily and without any problems.
The collateral
The units are operated at normal pressure.
In the event of an abnormal temperature increase or a breakdown of the ventilator, the distillation process is automatically stopped immediately. All units naturally bear the CE mark.
Vacuum distillation – (optional)
When connected to a pneumatic vacuum generator, the units can distil under vacuum.
Vacuum distillation lowers the boiling temperatures. This mode of operation is highly advantageous for solvents with boiling temperatures of >200°C, as well as for heat-sensitive solvents (chlorinated solvents), as it prevents the solvent from decomposing.
Fields of application
graphic arts industry, coachbuilding, chemical industry, leather industry, electronics industry, pharmaceutical industry, wood industry, metalworking industry, goldsmiths, paint, resin and plastic processing companies.