05/03/2025
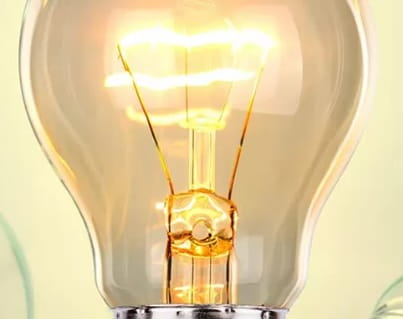
Nadelstiche in der Pulverbeschichtung: Ursachen, Auswirkungen und Lösungen
Pinholes in powder coating: causes, effects and solutions
Pinholes are small, needle-like indentations or holes in the powder coating that can affect the aesthetics and protective function of the surface. They often occur in thicker layers and are particularly visible on glossy or smooth surfaces.
Common causes of pinholes
- Substrate outgassing: Porous or galvanised materials can release gases during curing, causing pinholing. :contentReference[oaicite:0]{index=0}
- Moisture in the powder coating: Improper storage or high humidity can cause the powder coating to absorb moisture, which evaporates during curing and causes pinholes. :contentReference[oaicite:1]{index=1}
- Contaminants on the surface: Residues of oil, grease or other contaminants can impair adhesion and lead to pinholes. :contentReference[oaicite:2]{index=2}
- Insufficient pre-treatment: Insufficient or incorrect pre-treatment of the workpiece can favour the formation of pinholes. :contentReference[oaicite:3]{index=3}
How to avoid pinholes
To prevent pinholes in powder coating, you should take the following measures:
- Thorough pretreatment: Clean and degrease the workpiece carefully to remove contaminants. Suitable methods include chemical degreasing or sandblasting. :contentReference[oaicite:4]{index=4}
- Controlled powder storage: Store the powder in a dry and climate-controlled environment to prevent moisture absorption. :contentReference[oaicite:5]{index=5}
- Use of devolatilising powders: For porous or galvanised substrates, special powder coatings with devolatilisation properties can be used to minimise the formation of pinholes. :contentReference[oaicite:6]{index=6}
- Optimisation of application technology: Ensure that the coating parameters are set correctly and use high-quality equipment from manufacturers such as Gema, Wagner and Nordson to guarantee an even coating.
- Check the curing parameters: Make sure that the recommended curing temperatures and times are adhered to in order to ensure that the powder coating is fully cured and to prevent the formation of pinholes. :contentReference[oaicite:7]{index=7}
By implementing these measures, you can effectively prevent the formation of pinholes and achieve a high-quality powder coating.
Discover our manual systems Contact us now