08/03/2025
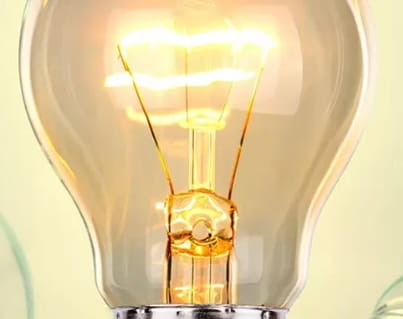
Schattenbildung in der Pulverbeschichtung: Ursachen, Auswirkungen und Lösungen
Shadow formation in powder coating: causes, effects and solutions
Shadowing occurs in powder coating when certain areas of the workpiece are not sufficiently covered with powder or when colour differences occur in the coating. This problem can not only affect the appearance, but also reduce the protective function of the coating.
Common causes of shadowing
- Unfavourable geometry of the workpiece: recesses, sharp edges and complex shapes can make it difficult for powder to reach certain areas.
- Incorrect spray parameters: Insufficient powder output or an incorrect spray angle can cause an uneven coating.
- Electrostatic shielding: Electrostatic charging can have an adverse effect on components that are close together or in deep corners.
- Lack of re-coating: Workpieces with complex geometries often require targeted re-coating to cover shadow areas.
- Incorrect grounding: If the workpiece is not sufficiently grounded, the powder cannot optimally adhere to the surface.
How to avoid shadowing
To ensure an even powder coating without shadows, you should take the following measures:
- Correct positioning of the spray guns: Use several spray guns or manual touch-ups to cover areas that are difficult to access.
- Optimisation of the spray parameters: Increase the powder quantity or adjust the spray angle to achieve an even coating.
- Use high-quality powder coating equipment: Gema, Wagner and Nordson equipment offer precise control options to ensure an even powder coating.
- Proper grounding of the workpiece: Ensure that the workpiece is optimally grounded to enable an even powder coating.
- Recoating complex geometries: If necessary, apply a second coat with adjusted parameters to cover hard-to-reach areas.
By optimising the application technology and using high-quality equipment, you can avoid the formation of shadows and achieve an even, aesthetic powder coating.
Discover our manual systems Contact us now